Blaauw kilns finally on campus
In Henrion Hall Wednesday morning, a Blaauw kiln is prepared for use. After a year of anticipation, three new Blaauw kilns have been installed in Henrion Hall.
Art students rely heavily on equipment to make their various creations. Ceramics students need everything from trimming tools to throwing wheels and kilns.
The School of Art, Design and Creative Industries at Wichita State has been working for more than a year to bring state-of-the-art kilns to the university.
Since summer 2015, Lindsey DeVries, coordinator of external affairs, has been working alongside the ceramics department and the Art and Design Advocates – a private WSU donor group for ADCI – to bring Blaauw kilns to campus.
Blaauw kilns are world-renowned kilns that are not on many campuses due to the high cost.
“The portion that we raised was only one-third of the funds, so part of the delay was assembling $150,000 from the university, from the college and from the portion that we fundraised,” DeVries said. “After that, those kilns were specifically designed for our space.”
Blaauw is located in the Netherlands, so it shipped the kilns by boat. Once the kilns arrived, the company sent representatives to help install them and hold workshops for professors to learn how to use them.
There are many top competitors when it came to selecting the right kilns, Ted Adler, associate ceramics professor and graduate coordinator, thought that Blaauw offered customizable features that would fit what the ceramics department needed.
“[Blaauw] came and I basically said, ‘Here’s our bottleneck points in the workflow during the semester, mid-terms and finals, here’s the kinds of research our grad students tend to do, here’s what we hope to allow them to do,’ and so they sat down and brainstormed and made a recommendation based off of what we were wanting,” Adler said. “They recommended three kilns to us and then because of our research emphasis we also got a gradient kiln.”
These four kilns allow students better control of how their projects are fired, and they can see the technicalities of how the process works. The gradient kiln allows for different temperatures on each sides of the kilns.
“For instance, when you fire a gas kiln, there’s the opportunity for the kiln to be uneven in temperature, so one part could be hotter and one part could be colder. Maintaining that evenness isn’t something you have to worry about with these kilns,” Emily Chamberlain, graduate ceramics student, said. “Turn-around work is able to get in the kiln and out of the kiln in a matter of 24 hours, and for a typical gas kiln that would be like a three-day process.”
These kilns are just the beginning for Henrion Hall renovations.
An ideas laboratory is set to be created within the building and Adler hopes for more improvements as well.
“I really hope that more renovations and repairs can be made to Henrion Hall,” Adler said. “This would not have been done if it wasn’t for them or for the vision of Royce Smith, the former director. I am so thankful for them and for their help, and excited to see how the department continues to progress.”
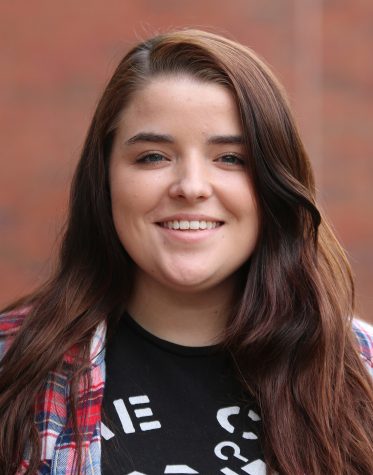
Marissa Campbell was the Culture Editor for The Sunflower. Campbell wrote music reviews as well as arts, culture and other entertainment stories. From...
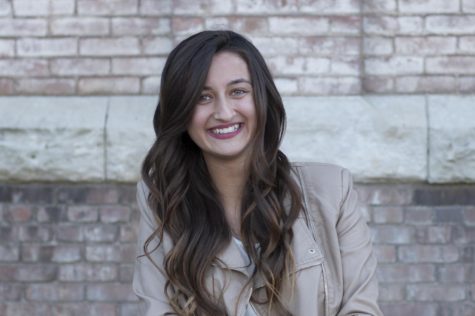
Selena Favela is a former photo editor for The Sunflower. She majored in graphic design. She is from Wichita, Kansas.